Meet The Maker: Fabio Giacomini – Handmade Surfboard Designer
For many people, surfing represents more than a sport. It is a way of life and a way to connect with nature and the ocean. Fabio, a Handmade Surfboard Designer and Shaper, was born in Rome on May 1, 1962. He has turned this passion into a lifestyle that led him from the Italian coast to South Africa, where he has been a resident since 2013.
With a scientific academic diploma in hand, this talented designer embarked on his career in the surfboard industry in 1980. He joined the first Italian surfboard company, West Coast Rome, where he refined his skills in design and shaping. In 1988, he founded Pike Surf Rome, his own company. It has been a cornerstone of Italian surf culture for over three decades. He has also collaborated with other renowned surfboard companies such as F22 Surfboard Durban and Bilt Surfboards Durban. Additionally, he has worked with Mistral Int throughout the years.



What inspired you to get into this industry?
I was born in a quaint seaside village in Rome. From a young age, I was captivated by the allure of the waves. Whenever I found myself at the beach, I would spend hours swimming and riding the waves on an inflatable mat. Then, in 1979, I acquired one of the first sailboards to arrive in Italy: A Mistral Competition.
It’s funny to think that now, because I am a designer and shaper for Mistral Int. I have come full circle. That sailboard was the catalyst that inspired me to begin crafting my own wave-riding boards. At the time, proper surfboards were non-existent in Rome, and I was determined to change that.
Can you tell us about a particularly challenging or rewarding project you have worked on with Entropy Resins products?
As a surfboard manufacturer, I have always been driven by the desire to craft high-performance boards. My goal is to create boards that stand out from the rest. For me, the thrill lies not in ramping up production for profit. Instead, it lies in exploring innovative ways to push the boundaries of surfboard design and technology. I am passionate about creating boards that not only ride the waves with precision. I also strive to offer a unique technical advantage over other boards on the market.
Over the years, I’ve introduced several innovations in my surfboard production. I constantly strive to improve the performance and durability of my boards. However, one of my latest developments stands out as a top modernisation in surfboard construction. I had the privilege of meeting and conversing with numerous surfing legends. One of them was Max Wetteland, who unfortunately passed away a few years ago.
During my visits to his surfboard blanks factory in Durban, Max and I discussed the best construction methods for high-performance surfboards. Our conversations were filled with valuable insights and shared passion for pushing the boundaries of surfboard design. In 2008, he suggested that the optimal construction for surfboards should involve the use of Polyurethane (PU) foam and epoxy resin glass. His recommendation emphasised the importance of these materials in achieving high-quality surfboard performance. He proposed the possibility of creating stringer-less boards with a specific layering technique.
The technique involves applying one layer at 0-90 degrees and a second layer at +45/-45 degrees, while carefully working the cloth during the glassing process. Max’s insights were invaluable, and I immediately began experimenting with his suggested construction method. The results were astonishing. I’m proud to say that this technique has become a hallmark of my surfboard designs. It offers exceptional performance and durability to my clients.

Despite all the advancements I had made in surfboard production, there was still one major challenge left to overcome. It was how to maintain the bottom rocker line before glassing. Without a stringer, the PU blank was incredibly flexible, which meant that glassing it after shaping could lead to deformities in the rocker curve due to the weight of the cloth and resin. It was a puzzle that took a considerable amount of research, experimentation and testing to solve. But after years of effort, I finally hit upon a solution that worked. In 2019, I proudly introduced the first-ever PU stringer–less epoxy surfboard glassed with Entropy Resins Clear Laminating Resin with Clear Extra Fast Hardener epoxy in my atelier in Rome, Italy. This ground-breaking achievement was the result of countless hours of dedication and hard work, and it has transformed the way I approach surfboard design and construction.
Thanks to a tool I personally designed and crafted, I was able to successfully launch the first version of my stringer-less polyurethane board. The tool, which I’ve named “To Go or Not to Go,” functions as a rocker curve copier. It can be adjusted to match the bottom-line measurements as shown on the project design software. This tool was essential in fixing the rocker line before glassing, a challenge posed by the flexible nature of the stringer-less PU blank.
The Building Process – Version 2.0 Stringer–less Board with Vacuum Technology
After hand-shaping the stringer-less blank, the surfboard artisan carefully carves a 1mm deep vertical track along the board from nose to tail. Next, they securely embed a carbon strip in the track and position their custom device, already calibrated to match the surfboard’s designated rocker curve, on top of it. Finally, they coat the strip with Entropy Resins epoxy to ensure a strong bond.
I have engineered my tool to withstand the force of tension as I press down on the glassed carbon strip. I leave the setup to cure for 48 hours, resulting in a blank shaped with a permanent rocker curve that precisely matches my design. This process ensures that the rocker curve remains unchanged during glassing, delivering consistent and reliable performance.
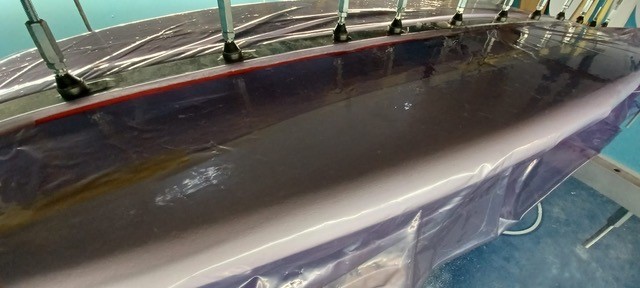
I recently updated my building process to the version 2.0 stringer–less board, which utilises the vacuum technology. A surfboard needs to remain flexible to express its technical features on a wave. However, Expanded Polystyrene (EPS) cores do not possess mechanical properties as strong as Polyurethane (PU). This is why professional surfers do not often use EPS boards in competitions.
In contrast, glassing a surfboard entirely using vacuum technology results in a stiffer board compared to one made through manual layup. Furthermore, vacuum-bagged boards may have increased vulnerability to breakage caused by buckling. To prevent breakage, a thick skin is necessary, which can be achieved through manual layup. By vacuum-bagging a whole board, the skin becomes thinner, causing the composite to become stiffer and inadequate. This can make the board more prone to snapping than one that is glassed using a normal hand layup.
If you only vacuum bag the carbon strip, used to reinforce the rocker line in a PU stringer-less board, you can increase the mechanical properties of the composite (PU/CARBON/ EPOXY) by 15-20%. That’s what I did for my new stringer-less surfboard. First, I vacuum bagged the composite material of PU/CARBON/ EPOXY, and then I applied a regular glassing layup with Entropy Resins Optically Brightened Laminating Epoxy with Extra Fast Hardener to complete the process. The result is a high-performing surfboard with exceptional mechanical properties.
I am a firm believer in the power of this new composite material, which represents a true innovation in the production and performance of surfboards. By combining the time-tested core material of PU foam (which still makes up 90% of annual HP surfboard production) with cutting-edge technologies such as carbon fibre and Entropy Resins epoxy, we can achieve exceptional results. While many developers in the field are exploring aerospace materials like cobalt cloth or varial foam, I believe that we can achieve even better performance by leveraging the materials that we have been using and testing for decades, plus finding new ways to combine them.
How do you incorporate sustainability and eco-friendliness into your surfboard building process?
In the past two decades, the global production of surfboards has surged thanks to the introduction of computer profiling machines. This has led to a significant increase in the number of boards produced each year by surfboard companies, particularly in the thriving Asian surfing industry. Despite these changes, my approach to surfboard production has remained the same for many years.
“My policy has been always: production by hand only.”
Enhanced with the implementation of new technology. Specifically, my shaping process has become more scientifically advanced, thanks to the utilisation of program design software. In the 21st century, relying solely on traditional hand shaping may result in less accuracy. Therefore, incorporating a shaping program into your workflow is essential. With the assistance of a project design software, you can effortlessly track and ensure precision by monitoring all the numbers involved in the process.
I believe that achieving better sustainability for a surfboard company requires a limited production model, focused on a quantity of surfboards that can be crafted by a select group of skilled artisans each year. This approach minimises the environmental impact inherent in mass production models that generate thousands of boards annually. Additionally, I’ve introduced some cutting-edge eco-friendly products into my limited surfboard production, including the use of Entropy Resins bio-based epoxy. By strategically combining a limited production model with sustainable materials, I’m committed to advancing the future of surfboard production in a responsible and sustainable manner.
What do you think sets your surfboards apart from those of other builders?
In the surfing industry, no one else is producing boards using the same technique as me. I utilise PU stringer-less and epoxy glassed with carbon vacuum technology. While some builders are using PU with a normal wood stringer and epoxy, the process of making a PU stringer-less board requires a great deal of skill and time. This makes it an inefficient option for mass production. Despite this, I firmly believe that the enhanced performance of the boards makes the extra effort and investment worthwhile.


To explore more of Fabio’s work, you can connect with him on his social media platforms listed below:
Website: Fabio Giacomini Handcrafted Surfboards



Explore other captivating surf-related articles:
To find out more about Entropy Resins visit entropyresins.com.