Trade Secrets: Guide to Mixing G/flex Epoxy with Other WEST SYSTEM Epoxies
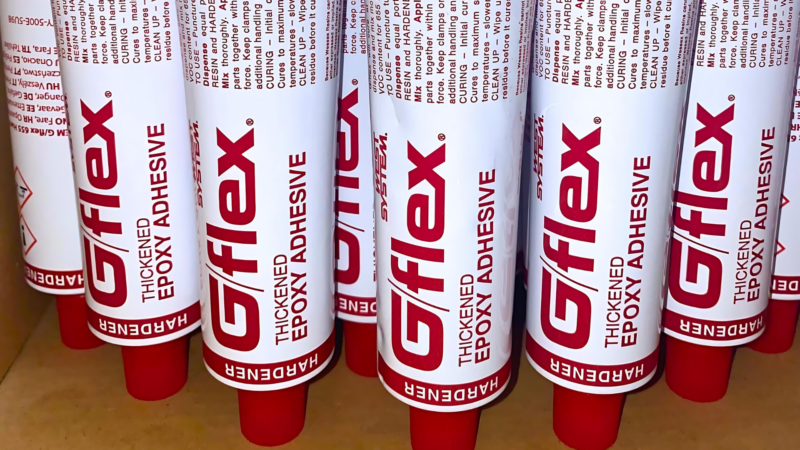
WEST SYSTEM® Epoxy is celebrated for its flexibility. Those with experience value the understanding of the fundamental attributes of WEST SYSTEM fillers, hardeners, and additives, as it allows them to customise and utilise them uniquely for their specific requirements. This manual will guide you on how to mix G/flex® epoxy with other WEST SYSTEM epoxies.
For years, seasoned users have been mixing the different products in numerous ways. For instance, users might combine 205 Fast Hardener® and 206 Slow Hardener® to create a hardener with an adjusted curing speed.
Benefits of Using G/flex Epoxy: Why Choose It?
G/flex epoxy notably expands the range of applications for WEST SYSTEM products. G/flex can be paired with WEST SYSTEM 105 Epoxy Resin® and one of its four standard hardener combinations. The outcome is a cured epoxy that is more flexible, capable of withstanding more deflection before cracking, albeit at a slightly reduced strength. The reduction in strength with G/flex epoxy is less pronounced than when using a low-density filler, but the increased flexibility does have an impact on ultimate strength. The table below provides a summary of how the properties change when G/flex epoxy is mixed with WEST SYSTEM Epoxy.
We’ve carried out a variety of physical tests on mixtures of G/flex epoxy and WEST SYSTEM Epoxy. The properties of the blended systems are proportional to the ratio of each product in the final mixture. Seasoned WEST SYSTEM users can trust their judgement to determine the desired ratio of each system to blend together, much like when they add fillers. However, it’s crucial to maintain the correct ratio for each system when mixing 105 epoxy resin with any of the WEST SYSTEM hardeners (By volume G/flex epoxy is 1:1, 105/205 or 206 is 5:1, 105/207 or 209 is 3:1). If the ratios are correct, there’s no need to mix each system separately before combining the two systems.
The same concept is applicable when combining G/flex epoxy with G5 Five-Minute Adhesive. In this situation, you’ll be making a trade-off between flexibility and strength in favour of a quicker curing process, relative to the proportion of each component in the blend.
CURED CHARACTERISTICS OF BLENDED G/FLEX 650 EPOXY AND WEST SYSTEM EPOXY | |
More G/flex epoxy | More WEST SYSTEM epoxy |
More Flexibility | Less Flexibility |
Less Strength | More Strength |
More Elongation | Less Elongation |
More Toughness | Less Toughness |
More Viscosity | Less Viscosity |
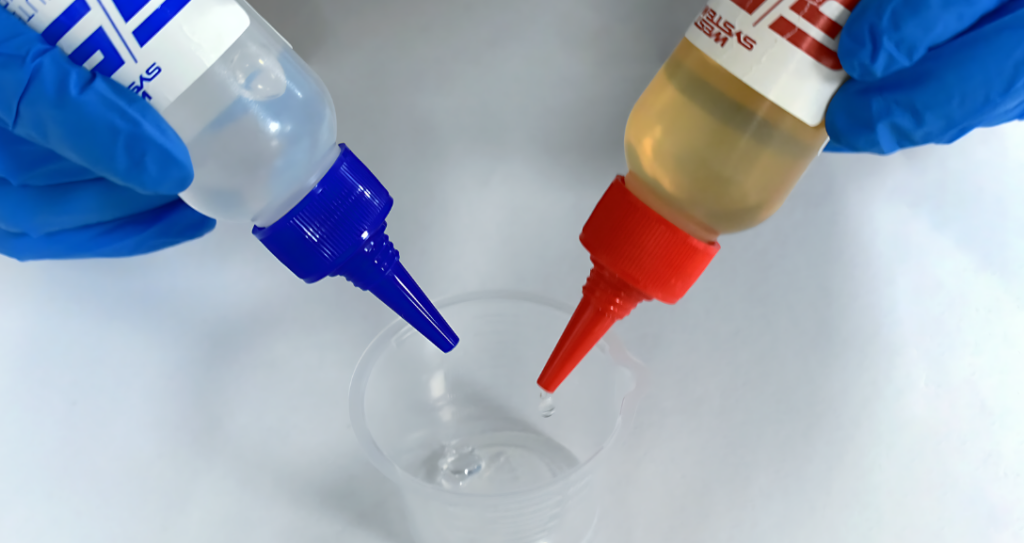
Glossary:
Flexibility – This term refers to a material’s ability to bend without breaking, which is quantified by its Modulus of Elasticity. A higher modulus indicates a stiffer material. It’s crucial to note that stiffness, which determines the deflection of a component under load, is not synonymous with the material’s strength.
Strength – This is the maximum stress that a material can withstand without failure.
Elongation – This is the extent to which a material can stretch under load, often expressed as a percentage of its initial length. The term “ultimate elongation” refers to the final amount of stretch a material undergoes before it breaks.
Toughness – This is a measure of a material’s resistance to fracture under stress. A material that is both tough and strong can resist fracture and absorb energy. However, a very strong material may be brittle and unable to absorb energy, while an extremely flexible material may not absorb energy because it deforms rather than bearing the applied load.
Viscosity – This term describes a liquid’s resistance to flow. While it doesn’t impact the properties of a cured material, it is crucial for application. A material with lower viscosity will typically saturate a fabric more easily, but it may not fill a gap effectively in a bonding application.
Have you subscribed to our FREE monthly newsletter? Sign up here!
Read other epoxy stories…
Working on a project? Share it with us! Click here…