Trade Secrets: How Can You Minimise Epoxy Waste?
In the days of each and everyone of us adapting our lives to be more environmentally friendly when working with epoxy, there is always a way to minimise your leftovers. David Johnson uses his many years of epoxy experience to offer insights into ways he has become savvy with epoxy waste.
What Techniques Does David Johnson Use in His Epoxy Work?
Working on Little Wing, a Sandhopper 19″ keel boat, David explains, I had just applied the final West System Epoxy finishing coats on a new modified wood/composite rudder I had made for Little Wing, and looked at the straining bag of waste, after I had swept away all the mess.
The rudder blank started life as laminations of Spruce, Mahogany and Western Red Cedar, glued with epoxy, shaped and sheathed in 300g/m.sq glass cloth.
I built a new rudder to replace one I had made in a similar fashion 10 years previously, but with a thinner foil section. We scrutinized the old rudder, which had weathered all that racing and time left on the boat. To our surprise, it bore hardly a mark and showed no signs of moisture seeping into its timber core. A great testament to wood/composite construction and its lifespan.
What Was The Process of Shaping Like?
I used a planer thicknesser and a circular saw bench to cut planks for the laminations from bulk board I had purchased, the sawblade lost 3mm of wood per cut, the thicknessing, a large pile of shavings, and the final aerofoil shaping of the blank a total of 1.3kg of wood taken off a 4.2kg blank.
The result filled me with immense pleasure. Working with cedar was a delight, and as I hand-planed a foil section with a razor-sharp blade, it yielded satisfying curling ribbons of transparent timber. The scent was reminiscent of the inside of a guitar, a sensory delight in the process.
I suppose I can burn the waste timber and shavings in the winter, but I looked closely at the other waste, pots, mixing sticks, roller trays, rollers, brushes, plastic squeegees and of course gloves.
I remembered my days in production Glass Fibre boat building, and recalled how we used to weigh the scrap bin at the end of the week, containing cured waste polyester resin, dry glass fibre, and cured laminate flashing from the trimming process. We weighed the scrap simply because, within it was raw material wastage, and importantly the labour content to manufacture it. At that time, we gave little thought to the fact that all this scrap would end up in a landfill.
What Role Does Work Planning Play in Minimising Epoxy Waste?
I consider myself frugal when working with epoxy, with experience I have come to know just how much mixed resin/hardener/filler I need to undertake the work I have planned, it’s amazing how much work a squirt of resin and a squirt of hardener will do.
I’m something of an expert at work planning too, so I have several epoxy jobs on the go at the same time, and also perhaps a chair that needs fixing if I have some waste. Strangely whilst building this rudder I was repairing a carbon fibre bicycle frame!!!! That is definitely multi tasking.
So with good work planning and estimating, it’s possible to be more efficient and not throw unrecyclable waste epoxy in the rubbish bin. From another perspective, meticulous work planning becomes crucial. Mix epoxy in the right proportion and it will cure, not waiting for anyone, man or woman. This creates an inherent motivation tied to the cure time. Just watch a team apply six osmosis coatings in a single day – their high motivation is palpable!
What Are Some of the Consumable Products Used in Epoxy Work?
Always opt for good quality pots of the same size. They not only define your working times but also serve multiple uses. If you carefully roll the sides of the pot and push on the bottom, you can break out the cured waste. Once broken, they’re ready for recycling! I have seen people all over the world using everything from yoghurt pots to sawn in half milk bottles, to baked bean tins to washing up bowls. I say if you want a good job, use the best tools, these consumables are part of your epoxy toolkit. It’s possible to throw your yoghurt pots in the recycling bag, but not when they are full of cured unremovable epoxy.
Are Mixing Sticks Worth It?
I once saw a production boat builder cutting mixing sticks from scrap ply at probably £ 40/hr, that was tragedy. Good hardwood stirrers and tongue depressor type mixing sticks cost barely anything, make mixing much easier, as you can get right into the corner of the pot…….remember that residue. I make a tongue depressor last for the day by simply using my gloves to wipe it as I dispose of them. A hardwood stirrer I will make last for a few jobs by cleaning it. We have now made a recycled plastic mixing stick/clean up tool that makes filleting and cleaning so much easier and will is reusable. Check out WEST SYSTEM mixing sticks here.
Epoxy is not expensive, but its not that cheap either, good tools make for good work and a little thought for work planning is hugely beneficial.
Find out more about safe epoxy disposal.
Have you subscribed to our FREE monthly newsletter? Sign up here!
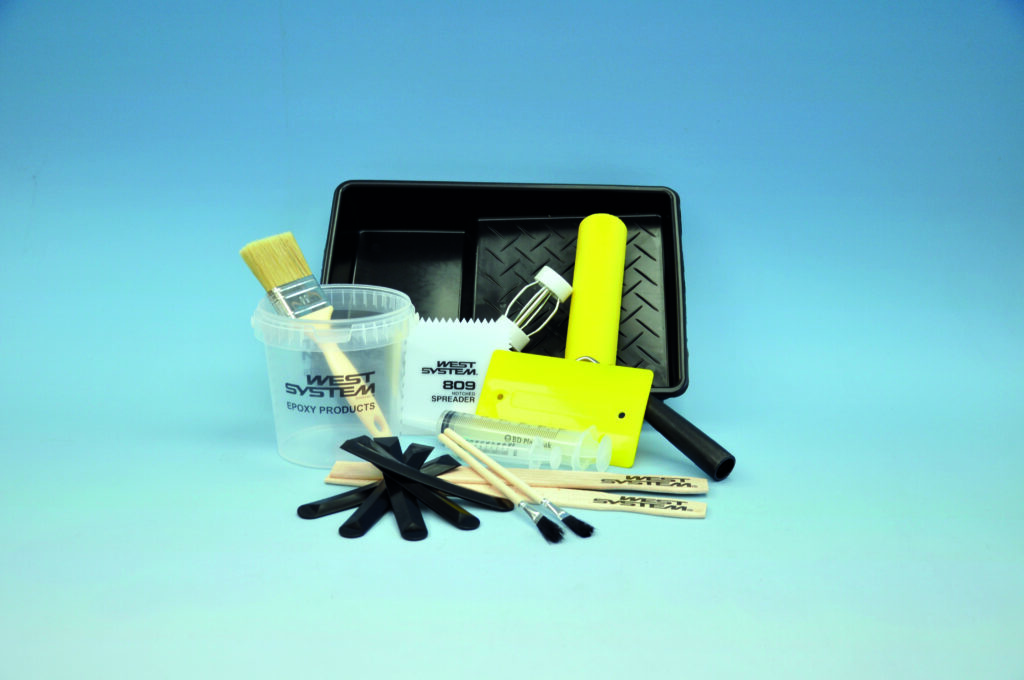
Working on a project? Share it with us! Click here…
Working on a project? Share it with us! Click here…