Trade Secrets: 3 ways to prepare a surface for recoating in epoxy
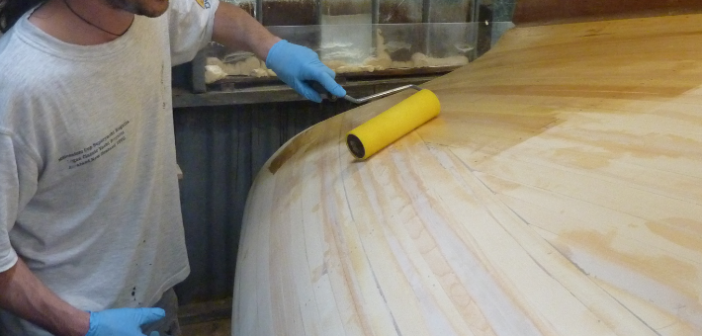
Whatever the project you’re working on, you’ll need several coats of epoxy resin and hardener. Most projects need between two and four. However many coats you’re planning on, you need to recoat at the right time and in the right way and ensure your surface is properly prepared.
How you prepare a surface for recoating with epoxy depends on whether the epoxy you’re covering is wet or dry.
If the epoxy is wet but cured enough to support the weight of the next coat, you can just apply another coat to create a ‘primary bond’, which is a bond between the epoxy layers at the chemical level (intramolecular bonding). However, as your epoxy blend dries it becomes harder to create a primary bond, so you’ll need to achieve a secondary bond (intermolecular bonding). Secondary bonding includes dipole-dipole bonding and hydrogen bonding. Mechanical bonding can also be achieved when liquid adhesive flows into surface cracks and cures, thereby ‘keying in’ to the surface.
Below, we talk you through the three main ways that you can get your epoxy-coated surface – whether wet or dry – ready for its next coat.
1. How to prepare a completely cured epoxy surface
If your epoxy has completely cured, then the first thing you’ll need to do is check the surface for amine blush.
Amine blush appears as a wax-like film on cured epoxy surfaces. It’s a normal by-product of the curing process and it’s easier to spot in cool, moist conditions. Even though amine blush can prevent bonding to further layers of epoxy, it is water soluble and easy to remove.
All you need to do is wash the surface thoroughly with clean water and an abrasive pad and then dry it with fresh paper towels to rub off the amine blush before it dries on the surface again. Then, sand any glossy areas of the surface with 80-grit sandpaper to ‘key it in’ and clean away the dust. Now you can apply your next coat of epoxy.
2. How to recoat a recently epoxy-coated surface: the sticky tape test
If you have recently applied epoxy, then you can apply the next layer when the previous coating has reached the sticky stage.
To check the epoxy is appropriately sticky, you can perform what we call the ‘sticky-tape test’. When you put your finger on some sticky tape, you can feel the stickiness but no glue actually comes away from the tape. Similarly, if you can put a gloved finger on your epoxy-coated surface and it feels tacky – but no glue comes away – then you’re at the right stage to apply another coat.
If a lot of epoxy comes away on your finger, then you’ll need to leave the surface to cure for a bit longer. By the same token, if there’s no stickiness at all then you’ll have to refer to method 1 above and treat the surface as fully cured.
3. Using peel ply
The third method for preparing a surface for recoating in epoxy is to use peel ply.
Peel ply – also known as release fabric – is a synthetic cloth that’s designed to improve the texture of an epoxy-coated surface. Importantly, it doesn’t stick to the epoxy; it just peels away to leave behind a perfectly textured surface that’s ready for your next epoxy layer to adhere to.
All you do is apply your epoxy blend to your surface and drape the peel ply on the top. Make sure you smooth the peel ply out with a spreader so that there are no air bubbles. Once the epoxy has cured, you can just peel off the peel ply and you’re ready to apply your next layer.
Remember that peel ply is best reserved for flat surfaces. It doesn’t work well with curves, as any wrinkles left in the peel ply will cure into the epoxy.
Thanks very much to Hamish Cook for his contribution.
Want to know more about coating surfaces in epoxy? Take a look through our detailed archive of Trade Secrets.