Projects: Making a 5,000-year-old pen
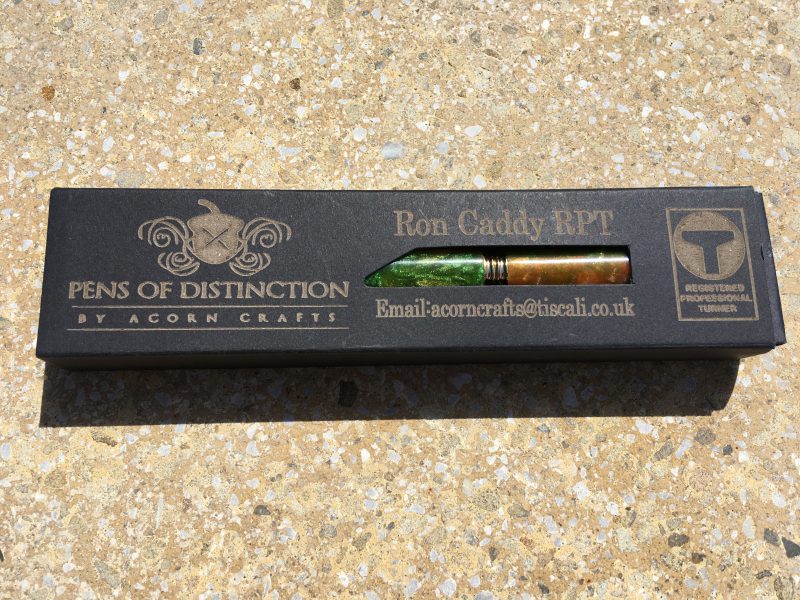
Penmaker and woodturner Ron Caddy specialises in combining ancient timber and modern epoxies to make exquisite – and affordable – custom pens. Ron is now making his latest creations with bio-based Entropy Resins® epoxy.
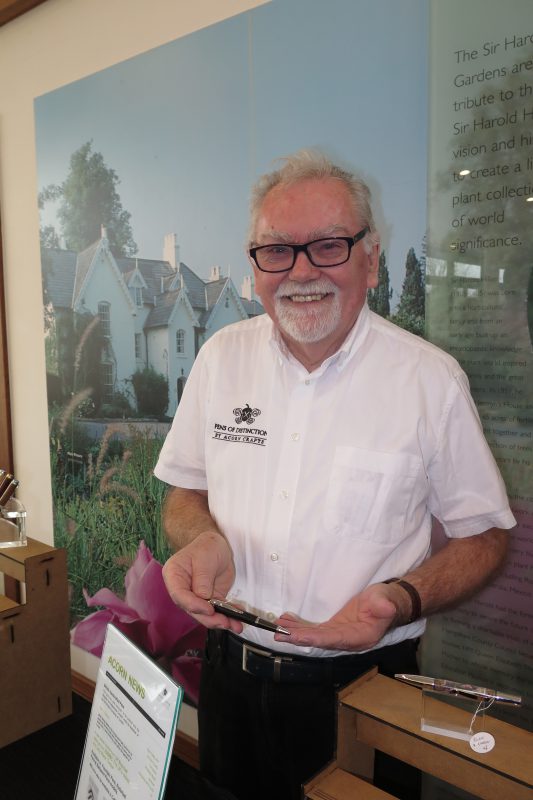
Ron Caddy of Acorn Crafts poses with a pen he made from timber that dates back to 3,300BC.
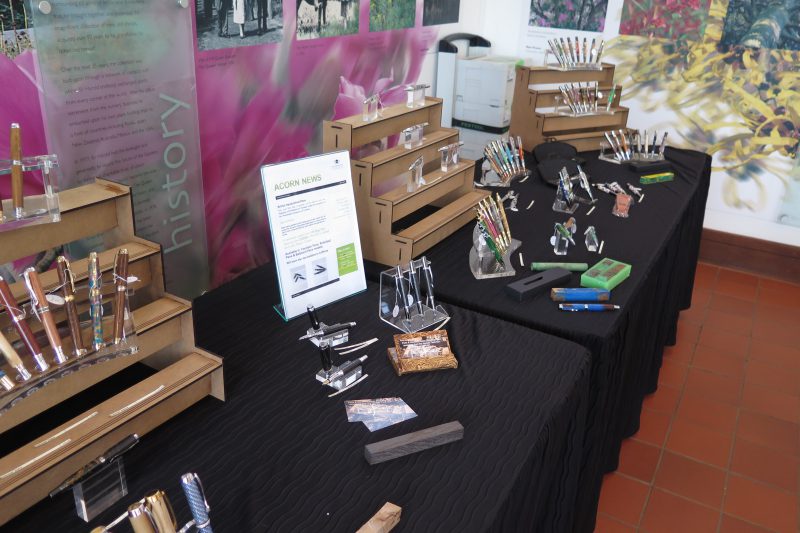
Ron’s range of hand-made pens is remarkable – some are created from epoxy composite, whilst others are turned from small rectangles of exotic woods. The metalwork and ink delivery systems are from established manufacturers, so the pens are totally reliable.
At a craft show near Romsey in Hampshire Ron Caddy was drawing a lot of attention to his display of custom-made pens. Whilst the inner workings of each hand-crafted piece are from trusted manufacturers, the magic is in the barrel and cap, each made in Ron’s small workshop in Alton.
The items on display ranged from pens coated in watch parts, with Ron joking that making them is ‘very time consuming’ to a remarkable piece made from preserved ‘bog oak’ dating from 3,300BC. Starting as rectangular ‘blanks’ they are turned on a lathe to form the cap and barrels, into which the workings are secured. With pens made from epoxy composites, Ron mixes a variety of materials into a silicon mould and then turns and decorates the result.
“Epoxy has so many uses in the creation of each piece,” he says. “I am still experimenting with various additives but have been very impressed with how modern epoxies allow such flawless results. I did worry about trapped air bubbles but by carefully following the manufacturer’s instructions this has not been an issue.
“My three biggest customers are all IT consultants,” Ron says. “There is something very special about a custom-made pen and I can make them exactly to a customer’s needs. Many of my pieces are given as gifts and I can include materials that have a special meaning to a client. The ‘watch’ pens, for example, can have the watch face set to a special time or date. In other pens I can include colours, minerals or timber from a special place, all encapsulated in epoxy.”
This image shows the basic production sequence of an epoxy-encapsulated pen. The raw materials are assembled into a silicon mould and then pre-mixed epoxy – possibly including additives and pigments – is poured over the top. The ‘blank’ for this blue pen, for example, has been made with a piece of rich red hardwood at each end. Once released the blank is rectangular in form and can be turned on a lathe with minimal wastage. You can see a turned blank as the green cylinder at the top right hand of the picture. The length provides enough material to create the cap and barrel.
The type of materials that can be incorporated into a pen is almost limitless. Here, acorns have been encapsulated, revealing their striking profiles as the piece is shaped on the lathe and inspiring Ron with a name for his company.
“You have to be quite careful when using the lathe on composites,” Ron says. “Unlike with ordinary wood turning, the epoxy composite has differing areas of hardness depending on where the chisel is striking. The trick is to anticipate some extra give where there is more epoxy and less where you strike pure hardwood.”
Watch parts are incredibly thin, so easily bent. This allows Ron to make these pens from a base blank, which once turned can receive the parts needed to create a unique pattern. They are tacked down onto clear epoxy and a second layer goes over the top to protect them.
“The hands need to have a gentle curve on them, so they don’t catch on clothing,” Ron says. “They can be set to an important time and to the exact minute – the birth of a child, for example. These pens are particularly popular.”
For a real piece of history, how about a pen made from bog oak recovered from the UK’s Fens of East Anglia? The distinctive dark timber is proven to be around 5,000 years old and was discovered in 2009 when the Fens began to be drained. The lowering water levels revealed a primeval forest that had stood on a particular site until the end of the last ice age. The fallen trees had been preserved within the highly acidic peat. Ron uses rectangular blanks of this rare wood to create a range of designs, typified by the fountain pen seen here.
“A pen has to be comfortable to use,” he said. “I machine these so that when the cap is screwed onto the back of the barrel – a process known as ‘posting’ – the whole instrument is nicely balanced and a pleasure to use.”
Find out more from Ron Caddy acorncrafts@tiscali.co.uk