Projects: Lively Lady update: Re-decked and painted
She’s looking good! Work on this historic vessel is now nearing completion, with a small team of volunteers giving up their free time to turn what was a gutted wreck into a yacht that is now in even better condition than when she was new!
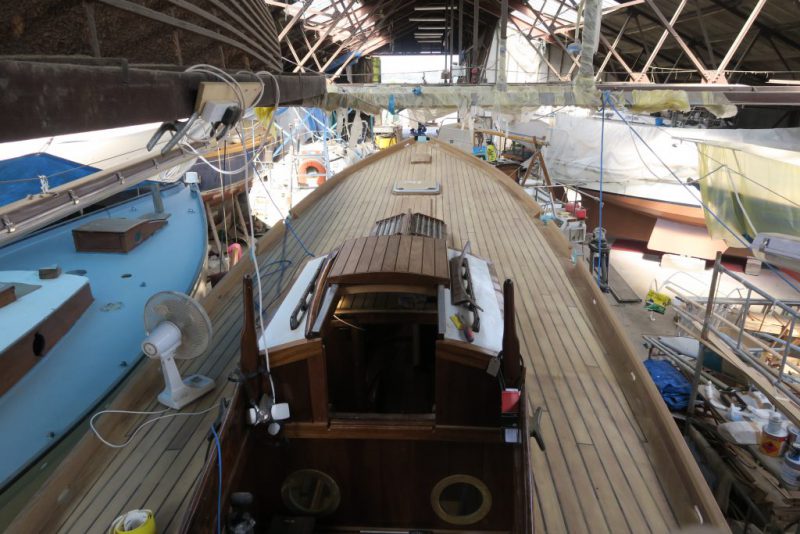
The iroko planks are now all caulked, with just the hatch left to do.
On Epoxycraft’s last visit on Friday 13th July 2018, we saw that all the iroko deck planks were all in place, caulked, sanded and just awaiting a few final details.
PRO-SET ADV-170/ADV-270 adhesive donated by West System International was used to bond the iroko onto a primed plywood substrate. Volunteer Steve Mason describes this versatile epoxy as ‘incredibly sticky – great stuff!’ and has since used it on a host of other bonding jobs that required a very high adhesive strength. These included building up the mast base and creating the forward toerails.
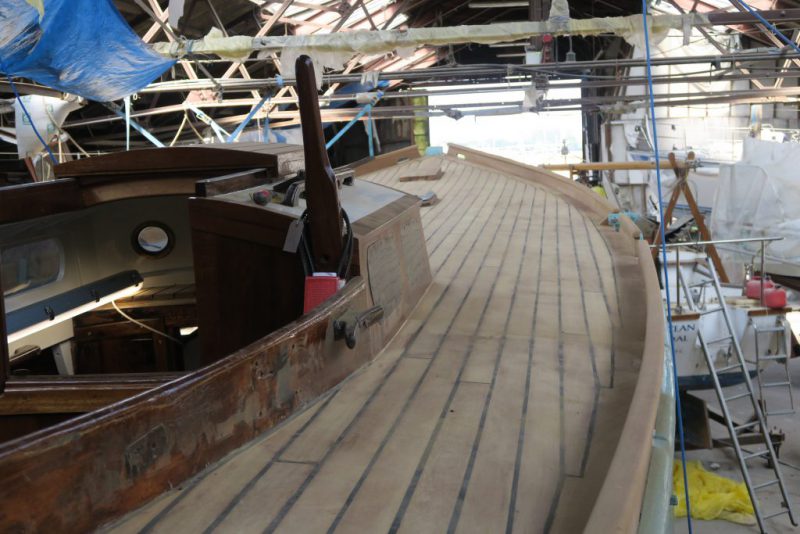
The sharp curve of the forward toerail was created by laminating thin strips of mahogany together in a former using PRO-SET Adhesive.
“We tried to bend the solid wood around the bow to make the toerails, but it just split open,” Steve said. “Instead, we simply laminated thin strips of wood in a ‘former’ (a curved jig) using PRO-SET Adhesive and a series of clamps. The result is a solid piece of timber that is incredibly strong, but with exactly the right amount of pre-formed horizontal bend.”
The team also used PRO-SET Adhesive to manufacture new wooden cleats, as they want the yacht to remain as close to the original as possible. Marine stainless steel cleats were a bit of a rarity in India in 1936, when the yacht was built.
“We made the cleats as basic wooden shapes in two halves and opposed the grain for extra strength. We then bonded them together using PRO-SET Adhesive. When the resulting piece was finished with abrasives, the result is a cleat with an invisible join and as strong as you like.”
Volunteer Carol Jenkinson has painstakingly stripped, primed and prepared the teak-planked hull before painting it with a custom ‘Lively Lady’ blue formulated for them by Jotun Paints.
Whilst there is still a lot to do, such as re-rigging and topside varnishing, the yacht already has her refurbished 12hp Beta engine back in and is nearly ready to be launched.
“Wooden vessels shouldn’t be out of the water longer than absolutely necessary,” Steve advises. “The planks can dry out and seams open up. We were due to finish in May, so we’re not too far adrift.”
The project has only been made possible by many hundreds of hours of work by the dedicated volunteers and the generous donations of product and expertise from the marine industry.
We’ll keep you posted as she nears the water.