News: Glen Lee River Table
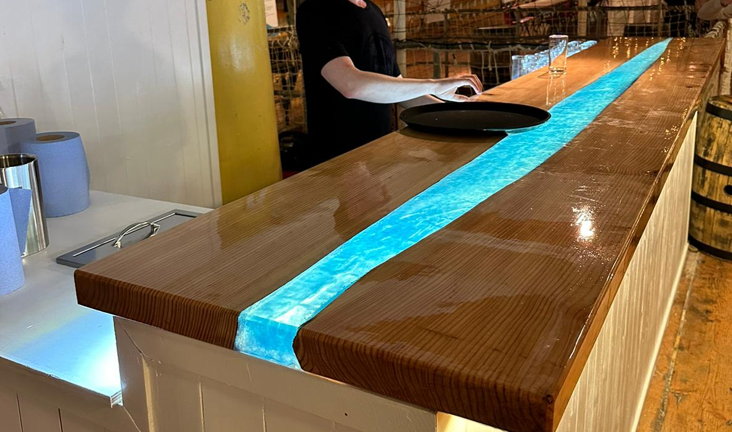
Volunteers at Glasgow’s Clyde Maritime Centre have made a stunning river table/bar and installed it in the Tall Ship Glen Lee, a three-masted museum ship that operates as a visitor attraction and events venue. The charity anticipates that the bar, made with Entropy Resins®, will attract more events like weddings, parties, and corporate functions, helping it recover from COVID and other current challenges like the cost-of-living.
How is Glen Lee a Symbol of Glasgow’s Maritime Heritage?
The Clyde Maritime Trust rescued her as part of the 1990s rebranding of Glasgow as a city of culture. Since her launch 126 years ago, she has had an incredible history. Italians owned her and installed her engines (under the name Clarastella). She served the Spanish Navy for sixty years (under the name Galatea) before being abandoned in Seville in the 1980s. After a fire onboard in the late 80s, she sank, and the Spanish Navy nearly scrapped her. However, they ended up selling her at auction. The Clyde Maritime Trust bought her. In 1993, after a nine-day tow from Seville, she was ‘patched-up’ in Greenock and regained her original name – Glen Lee.
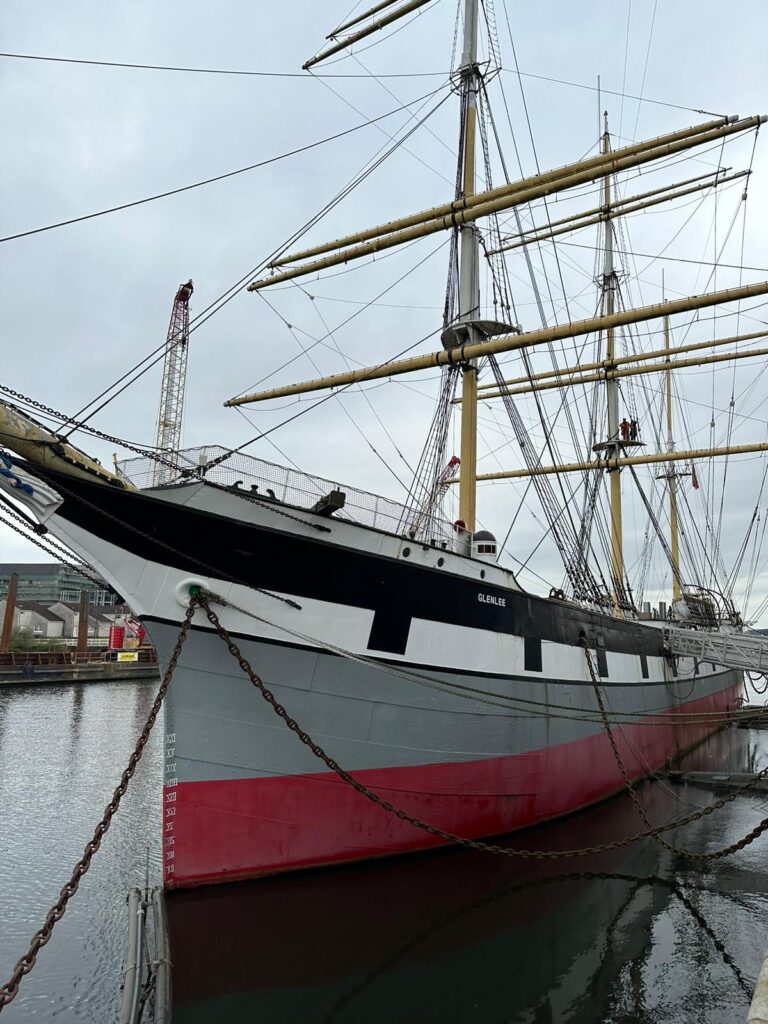
What was the Impact of Covid-19 on Glen Lee and the Maritime Centre?
Lachlan Cunningham, the Workshop Manager, says that even though they lovingly revived her in Glasgow, the ship suffered during the COVID furlough because she requires constant attention. Water seeped through her deck and devastated her in four months. According to Lachlan, she had ‘gone to rack and ruin’ because the deck needs constant re-caulking to maintain its integrity.
Prior to covid, Lachlan was running a volunteer programme to teach traditional maritime skills. The focus, working with six different charity partners to help build volunteers’ confidence and skills, had been on building a variety of boats like traditional clinker dinghies, St. Ayles skiffs and a 40ft motor cruiser. Those projects were using a lot of WEST SYSTEM® Epoxy, supplied by Wessex Resins which also manufactures PRO-SET® and Entropy Resins epoxies under license from Gougeon Brothers Inc.
After COVID, the disappearance of visitor funding streams tightened the budget. As a result, they decided to redirect the volunteers from building traditional boats to undertaking capital improvement projects. These major, mainly utilitarian, projects aimed to secure the ship’s future. They included the addition of a sprinkler system and an awning system to protect Glen Lee from UV. However, everyone welcomed the bar top, an aesthetic project, as a great challenge.
How is the Bar Significant for Glen Lee’s Survival?
“When the ship first came back, the first thought was that it should be returned to how she was when she was made,” says Lauren Henning, Learning and Museum Manager. “But, the ship survived all these years because she adapted. We need this bar to help generate income which means we can tell her story and keep her life going. Adapting means we can carry on her history.”
The bar top – measuring 4 by 0.6 metres – was made from “a chunk of timber from five and half years ago,” says Lachlan. “We previously made a captain’s gig from scratch, using Scottish Larch. The bar is the other half of the keel of that boat.” The latter currently sits on the main hatch of the Glen Lee.
He says he was excited to use Entropy Resins Clear Casting Resin and had done a little trial, making an inch-thick coffee table. But for the bar top, the pour was considerably bigger.
“This was a 28 litre pour, 54mm deep (right on the depth borderline). It took three days in total for the resin to cure.”
How was the Varnishing Process Conducted for the Bar Top?
“We decided to varnish instead of oiling the top as it’s a bar top and is going to have constant spillages – we can’t plan for what people will do, so we decided to tie the entire top together with gloss and yacht varnish.” This was after sanding to 240 grit. “As soon as we wet it with varnish, it popped. It was incredible watching it come to life.”
“The varnish took two weeks to apply using a two-part high-build sealer topped with a high-performance two-part yacht varnish, for a total of eight coats.”
Volunteers built the carcass of the bar in the workshop. They bolted the top on in the vessel, which features LED strip lighting on and under the bar top. The bar also has a mirrored box underneath the epoxy river that uniformly lights the whole piece.
How does the Bar Blend with the Existing Aesthetics of the Ship?
“From an aesthetic point of view, we didn’t want a spaceship in the middle of the ship,” says Lachlan. “So, it uses tongue and groove cladding to tie the bar into the existing walls. You forget it wasn’t always there.”
“At night it’s a different landscape, with fairy lights and candles. The bar leans into that.”
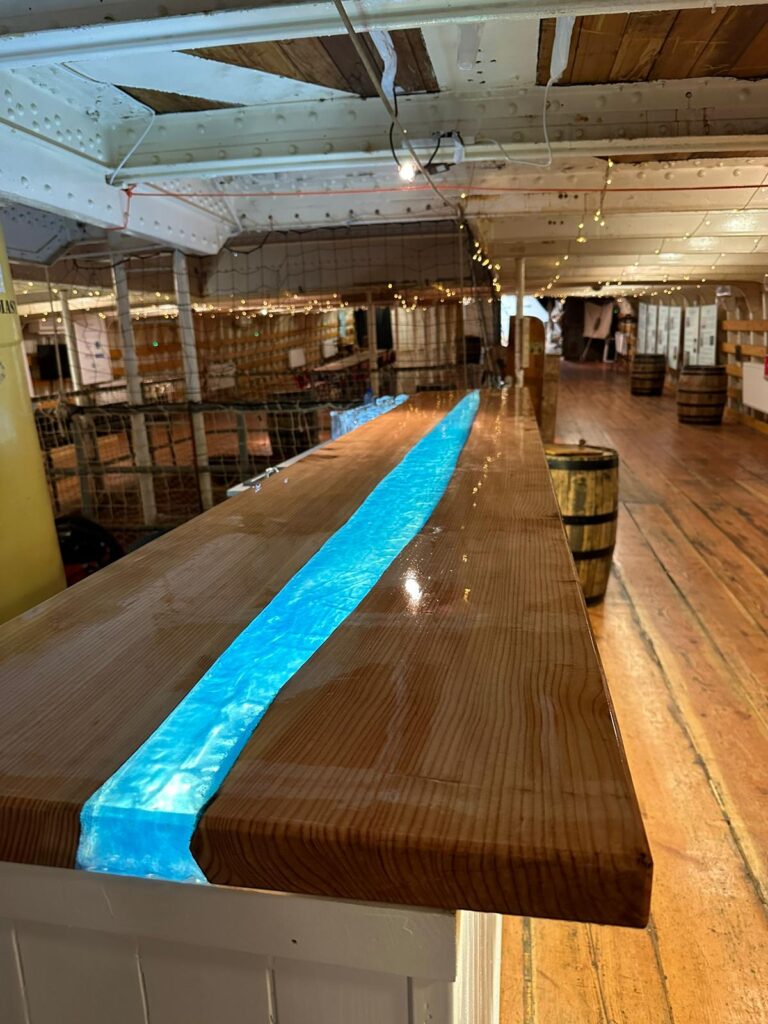
The team used a metallic pigment as the staff consensus was that it needed to shine. All staff including volunteers came to watch the pour and the team says they’d love to build another one. “But I need a reason,” says Lachlan (the workshop takes on contracts for projects, with money going back into programme).
In the meantime, the bar takes pride of place in the depths of the ship. “The sailors would have loved it,” says Lauren.
Lachlan can’t praise the team from Wessex Resins enough for the help and support which was given during the bar top build – and previous projects. “They’re always at the end of the phone,” he says, “or here in person to see how we’re doing. The support is like the products they manufacture – phenomenal.”
Find out how to visit the Tall Ship Glen Lee and/or host an event there thetallship.com. Details of Entropy Resins range of biobased epoxies can be found HERE.